From China to the world – how the global ambitions of China’s EV makers are reshaping supply chains
Building on their domestic success, China’s electric vehicle makers are increasingly looking further afield. But as they react to trade tariffs, supply chains are on the move too.
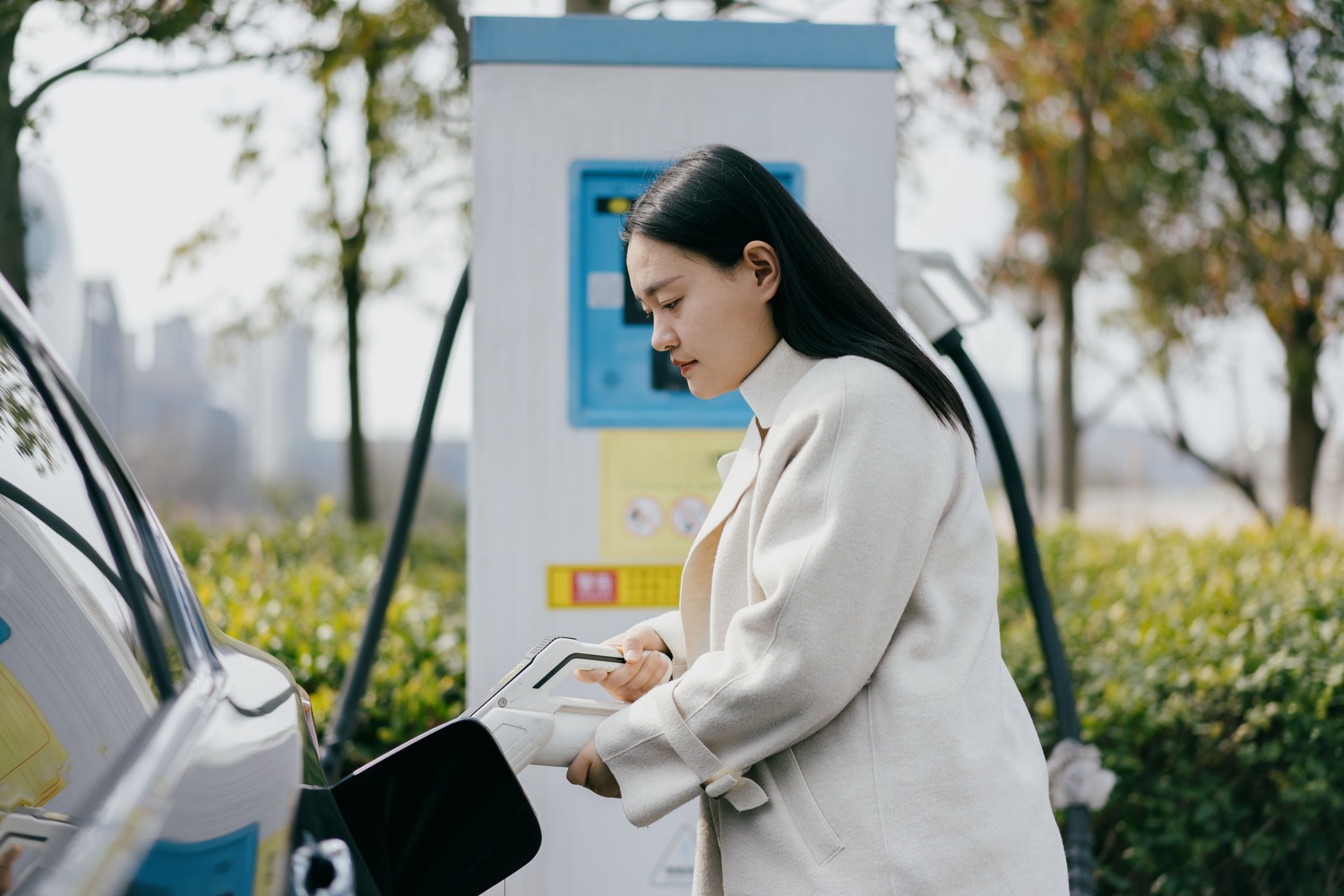
If you live outside of China, or Asia more broadly, the electric vehicle (EV) company BYD may not be one you’ve heard of.
More familiar brand names such as Tesla tend to capture much of the attention and cachet, while electric models produced by established automakers have higher brand recognition.
But at the end of 2023, BYD knocked Elon Musk’s company off the top spot as the world’s biggest EV maker. The home-grown Chinese brand has rapidly come to dominate its domestic market, making up over a quarter of the market share. China is now home to more than half of the EVs on the road today.
As an early adopter of EVs, supported by favourable pricing and government policies, sales in China continue to boom – over one in three new car registrations in the country in 2023 were for electric cars. However, Chinese automakers are increasingly looking outwards, seeking expansion and maximising the opportunities given by the country’s dominance of battery manufacturing.
Europe is a key market for Chinese EV exports, but increasingly countries in Latin America are also emerging as destinations. And, of course, many locations closer to home in South Asia are being targeted.
But, with several countries imposing punitive tariffs on Chinese EVs, the supply chain is in flux. While some companies are exploring nearshoring as a solution, emerging new players are rethinking their logistics play.
The particular challenges of EVs
DP World has been focused on the automotive industry for some years and continues to adapt its business in line with these shifting trends. Compared to other types of goods being moved, vehicles are particularly high-value and represent a large amount of capital invested by the manufacturers. This makes an end-to-end service with a wide geographic reach particularly valuable – especially given the local connections and expertise DP World has in each of its hubs.
Another notable challenge with EVs is that restrictions around their batteries often mean they need to be transported as ‘dangerous goods’ (DG). This means there may be different requirements placed on shipments compared to traditional internal combustion engine (ICE) vehicles, and the logistics can be more complex. Special licences are required for storage and transport,
for example, and the processing time and documentation can be rather different across different markets.
In addition, in current shipping markets, space for ocean vehicle freight has been quite tight as RoRo capacity struggles to keep pace with demand. And there is even more competition for the limited space available for DG.
The impact of tariffs
For many Chinese automakers, the imposition of tariffs by countries such as the US and EU has caused them to rethink strategies. Some are exploring assembly and manufacturing set-ups in Eastern Europe or Latin America. New markets such as North Africa are also emerging as supply chains react to policy implications.
Meanwhile, many manufacturers are increasing their exports to beat the tariff deadline, adding further strain to logistics along some routes.
Supply chains will remain dynamic as the impact of tariffs starts to take effect.
New solutions
DP World has been working with customers to overcome these challenges. For one major Chinese carmaker, we found a new route into Europe using our P&O ferry network in Zeebrugge, for example. This bypassed the congestion and shortage of space at other terminals and yards and created a faster route to end customers.
When it comes to sea crossings, RoRo currently dominates automotive logistics, but DP World is focused on building cars in containers (CIC) as an alternative option. The advantages are clear. Firstly, using container ships increases capacity and availability. And secondly, because a container ship can carry more cars stacked in containers than a RoRo vessel, it is a more environmentally friendly option.
Only around 20% of our cars are currently transported as CIC, but it is increasingly being explored by some of Asia Pacific’s new generation of EV manufacturers.
More broadly, the ability to lean on other intermodal solutions like rail freight and road transport across the DP World network has proved advantageous for several customers.
One new EV manufacturer, for example, was looking for support shipping cars from China to Laos. This presented particular challenges given Laos’ underdeveloped logistics infrastructure compared with other routes into Europe, and the manufacturer had previously experienced a high level of damage in transit. DP World offered a range of solutions including cross-border road and rail options and CIC, which significantly improved the manufacturer’s access to the land-locked country.
The traditional vs the new
While many established automakers have expanded into the EV market in recent years, a number of new players have also entered the space. This next generation of EV makers comes without the historic supply chain structure built over years of moving internal combustion engine (ICE) vehicles. And this is heralding new approaches to logistics as fresh thinking brings novel solutions.
One example is how new EV makers have embraced DP World’s racking system for wrecks, where up to four vehicles are transported on racks in containers. In this way, cars can be recycled more efficiently and cost-effectively, which contrasts with the traditional ICE vehicle approach, where old and broken models go to waste.
Technology provides greater visibility
As Chinese automotive manufacturers increasingly look further afield for opportunities, the need to track vehicles and bring predictability to logistics becomes more pressing. And this is where technology can help.
DP World’s inventory management system helps bring greater transparency and control to supply chains. With warehousing and transportation management systems connected through a suite of technologies, cargo owners and manufacturers can make better decisions about the production and delivery of their vehicles. Supply chains can be more efficient and less wasteful, too.
As Chinese automakers increasingly assert their dominance on a global scale, EV supply chains continue to evolve. And despite the challenges posed by tariffs and complex logistics, they are leaning on innovative solutions to maintain their competitive edge.
The importance of robust and adaptable supply chains cannot be overstated as Chinese EV makers expand their reach to new markets in Europe, Latin America, and beyond. This dynamic environment underscores the need for constant adaptation and innovation in the logistics sector to support these thriving manufacturers.